Last Updated on August 14, 2022
Our world is changing very fast. And with rapid innovation and fast technological transformation, every industry, city, government, and community are facing new challenges regularly. But along with these challenges come new opportunities.
And as things are moving fast and complex infrastructures are becoming more and more connected and digital, we are generating more and more data every day. It is estimated that 2.5 quintillion bytes of data are generated every day.
And with 5.03 billion internet users, 4.65 million social media users, 13.1 billion IoT devices, 6.5 smartphone users, and all the internet-connected devices that we interact with regularly, it is expected that by 2025, 175 zettabytes of data will be generated every day.
With all this data, data scientists and IT professionals can create a digital equivalent of assets that give possible what-if scenarios. Thus digital twins are becoming the pillar of innovation, creating virtual representations of real-world products, systems, infrastructure, or even entire cities. But what exactly are digital twins?
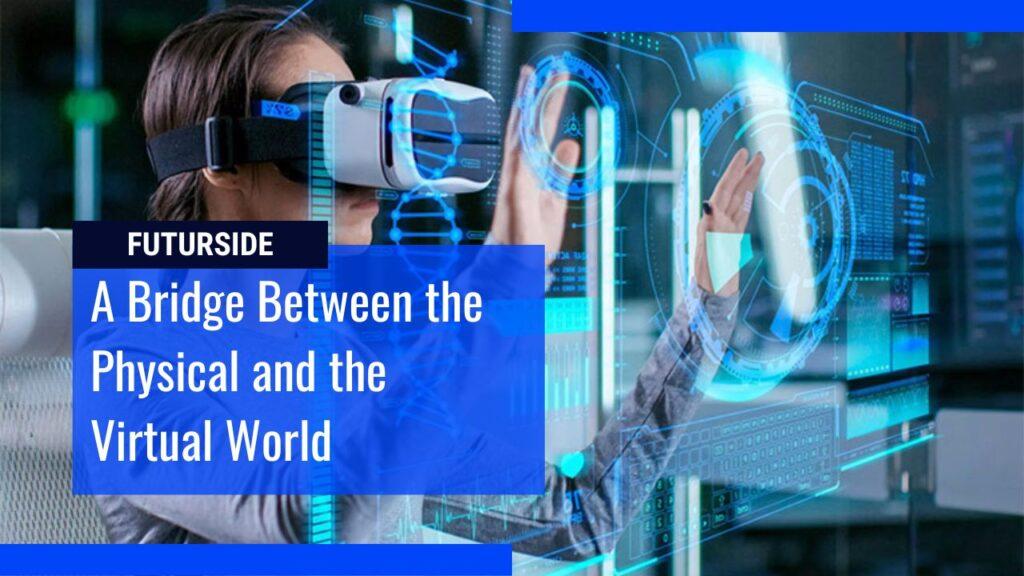
Contents
What is a digital twin?
A digital twin is a virtual replica of a real-world object/asset. They are a digitalized representation of physical products, machinery, or process used to predict and optimize the performance of the product in different scenarios.
Digital twins are used to simulate different scenarios before they happen in real life. This helps companies save time and money by predicting any unpleasant surprises that could have been avoided.
The process of creating a virtual replication of assets involves specialized developers who are often experts in data science, applied mathematics, and IT professionals.
They begin by researching the physics of the mimicked object and then use real-world data to create a mathematical model. This digital replica then acts as a representation of the real-world model.
Once the model is created, it can be used for various applications, including predictive maintenance, fault isolation, and anomaly detection. These models are created to improve products and prototypes.
Moreover, they are a great way to study the underlying physics of a physical product. Building a digital copy of a product is an essential step in the process of product development. It’s vital to understand the entire system before it starts manufacturing.
To create a virtual replication, data about the physical item must be collected. The data is used to represent the current state of a product and its operational history. Digital twins are logical constructs and the data come from multiple applications.
While it is still rare to create a full-scale replica, digital twins have many benefits and can be used for various applications. They are used for various applications in different industries.
From offshore wind turbines to improved racing cars, virtual replication can be used for solving a wide range of challenges. They are also used to model infrastructure and investigate workflows and staffing.
Why digital twins is important?
The concept of a digital twin is nothing new, but it’s only now starting to catch on. The benefits of using computerized models are numerous. These models can be used for asset management and maintenance. This can save money and improve the quality of products.
The digital twins market size was estimated at use 6.75 billion in 2021. It is projected that in 2022 this number will reach USD 8.88 billion. The market size is expected to increase exponentially by a CAGR of 40.6% between 2022-2029. By 2029 the market size will reach USD 96.46 billion.
A digital twin can be used to duplicate physical objects. Hence it can also be used to simulate the performance of highly instrumented devices. A computerized version can also help predict future performance.
It can also help companies improve their products’ design. It automatically collects and analyses data to provide relevant insights into assets. As more data become available, the digital twin becomes more accurate.
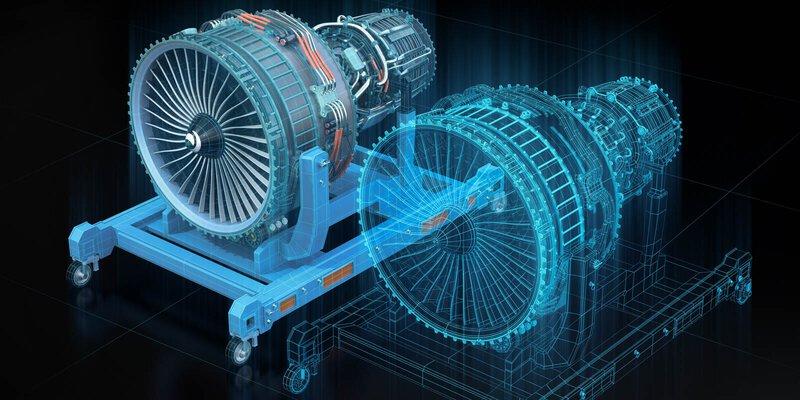
There are many applications of digital twins for industries that deal with physical objects. It can also help create a personalized experience for consumers. In addition to enhancing customer experience, a digitalized copy can be a valuable asset for companies.
When used in manufacturing, they can help products run at peak efficiency. It can also help manufacturers identify end-of-life products and determine which materials can be harvested. It can also improve efficiency in mammoth engines and complex machinery.
The list of uses for virtual models of a physical object grows every day. They can be used for many things, including trains, aircraft engines, offshore oil platforms, turbines, and cars. The same technology can be used for maintenance. Technicians can test and propose fixes before implementing them in a real product.
Type of digital twins
There are different sorts of digital twins relying upon some degree of item amplification. The greatest contrast between these twins is the area of utilization. It is normal to have various sorts of computerized twins coincide inside a framework or cycle.
- Component Twins – These are the essential unit of computerized twins, it is a small illustration of a working part.
- Asset twins – This one is when at least two parts cooperate. Asset twins let you concentrate on the connection of those parts, making an abundance of execution information that can be handled and afterward transformed into noteworthy bits of knowledge.
- Unit twins – this one empowers you to perceive how various resources meet up to shape a whole working framework. Unit twins give visibility in regard to the association of resources and may recommend execution upgrades.
- Process twins – This one uncovers how frameworks cooperate to make a whole presentation of a facility. Process twins can assist with deciding the exact timing plans that eventually impact general adequacy.
Impact of digital twin
It can be used to improve manufacturing efficiency and product performance. This technology allows you to capture real-time data to identify and correct inefficiencies.
A digital twin is a powerful tool for analyzing data from many different sources. It can also be used to improve quality control and management. It can simulate the undergoing events of an actual product and give feedback to determine whether the model is accurate.
Combined with machine learning, the results of this process can lead to better business decisions and more profitable products. Machine Learning is a subdomain of artificial intelligence that process, learn, and adapt from the data it is fed with. And by doing so it improved itself.
A virtual twin can also eliminate human bias. Using a virtual replication can provide a single, logical view of the actual situation. Then, the information can be derived from evidence, probability, and analytics.
Furthermore, it can provide a deeper analysis of manufacturing plants and factory systems. This type of analysis can be critical for incorporating innovations. As a result, digital twins are a valuable tool for improving productivity and increasing profits.
Virtual models are used to make smarter decisions and improve business operations. They can also be used to optimize business processes. If you are a manufacturer, it will be easier to know what needs to be built or maintain when you have a digital representation of assets.
You can choose which parts to harvest and which materials to discard. It can also improve customer experience. With the help of digital twin technology, you can make smarter decisions and even save money by reducing costs.
By creating a virtual equivalent of the physical object, engineers can assess the likelihood of failures before it even leaves the lab. Furthermore, having a computerized version of the physical object is beneficial to both customers and employees.
This technology makes manufacturing more efficient, safe, and cost-effective. Digital twins models can help to identify performance issues to optimize processes and services.
Virtual twin is becoming a key element of modern engineering and is being used to develop prototypes for new products and processes. It can simulate a whole factory or individual machines. The benefits of digital twin technology are many.
Benefits of digital twin
The use of digital twins can help reduce development and production cost. This tool also enables engineers to test products before they are put into production. They can perform complex analyses and synthesize various scenarios before they affect actual production.
Moreover, these technologies can help improve risk assessment and speed up product development. As a result, companies can improve their production line reliability, minimize machinery downtime and maximize their productivity.
A virtual clone allows engineers to simulate anything in the physical world. This feature is especially useful in manufacturing, as large forces can be problematic for robots. A virtual twin can compensate for this problem by keeping robots on the milling path.
It is possible to compare sensor data of a real point with the simulation. A digital replica also lets companies plan the availability of parallel operations which reduces the risk of failure. Hence, they are an ideal solution for improving manufacturing processes.
Another benefit of a digital twin is that it is a tool that allows collaboration among service professionals. Professionals can access information about the performance of a system in real-time. The result is a consistent service process.
Consistent service processes enable engineers to evaluate the performance of their systems. Which leads to more effective and efficient decision-making. Digital-twin allows engineers to identify and mitigate problems before they affect production by debugging processes before they are executed.
The virtual clone also helps businesses to predict future maintenance costs and improve their products. Moreover, it allows for faster time-to-market product development. As a product is developed, it can be improved quickly and without the risks of failure.
For instance, it helps a company make predictions based on the actual behavior of the system in question. By modeling the entire process, the digital twins can provide predictive information for better maintenance and improved product development.
Because the computerized version is connected to real-world data, businesses can predict implementation challenges and even anticipate potential problems before they happen. A virtual clone also validates the functionality of a product and allows for rapid improvement.
Technology of digital twin
The digital twin is an innovative concept that fuses make use of advanced technology such as the Internet of things (IoT), Artificial Intelligence (AI), Machine Learning (ML), and Augmented and Virtual Reality (AR/VR).
These technologies are used to create the virtual representation of assets. Where IoT is used for the collection of data, AI is used to process the data and AR/VR is used to visualize the replica of the asset.
Machine learning algorithms are used to seek patterns from the data it is fed. And by doing so the algorithm learns and adapts thus improving itself progressing. The more accurate data it is fed with the better it gets at detecting anomalies and it can also suggest corrective measures.
The rise of internet of things devices is making virtual replications possible because they are collecting huge amounts of data in our environment. Globally many companies are already focusing on implementing digital twins in their operations to improve processes.
To create a computerized replication, a large volume of data needs to be collected and processed. This can be done with our current 4G infrastructure but with 5G networks entering the mainstream the process will be further enhanced.
5G will allow the collection of massive data sets. It will also process data faster and reduce. Latency will also reduce thus allowing faster response time. Edge computing will further enhance digital twin technology by providing in-house computing power.
With more advancements in ML, AI, and data analytics, these virtual models will drive more innovation and improve performance. The convergence of the virtual and physical worlds is imminent, and the digital twin plays a vital role in this process.
Future of digital twin
The future of digital twins is brimming with possibilities. These models of physical objects can act as measurement, control, diagnostic, and production units. They can also provide insights to help companies make better decisions.
In the past, companies have to rely on physical plants to simulate their processes which is a costly and time-consuming endeavor. But now, experts are using virtual twins to improve the reliability of complicated processes.
Developing a digital twin can be a powerful and important tool for any business. Ultimately, it will change the way we live. It will revolutionize the way we work and build. Using a virtual clone can save companies money by minimizing unnecessary expenses.
With it, companies will be able to make better decisions. The digitalize version of a physical object will be a replica of a physical one. The computerized model can then be used to test various settings and tweak components to achieve optimal performance.
This is an efficient method that can dramatically reduce the cost of prototyping. And digital twins can be shared across departments, they can help companies understand usage and make more informed decisions about how to price their products.
While digital twins are still in their infancy, they have already started changing the face of different industries. Today, the technology can be used to design any asset and can be connected to various other assets, from smart cities to healthcare.
There are several key design considerations for virtual twins, which should be incorporated into the software and hardware systems. If these considerations are considered, the future of digital-twin applications will be bright and prosperous.
Creating a virtual replication has become a reality in many sectors. The early uses were expensive and limited to highly valuable assets. However, the availability of cheap and prolific technologies has lowered the barrier to entry and made it possible to implement such a system.
It is now a viable tool for many industries and will make data collection more efficient. While the concept of digital twins is a promising one, the near-term challenges are a concern.
It requires a complex process to create a digital version of the physical object and it can be time-consuming. Businesses need to choose the right technology for their IoT endpoints and develop a framework for processing the data.
Another challenge of digital twins is the security of the data. It is essential to keep the information safe and secure when storing critical data. The virtual replica can be a very useful tool in manufacturing but it can be difficult to maintain.
While these challenges are important to overcome, the benefits of a digital twin are well worth the effort. What’s more important is that the digital twin continuously evolves, thanks to the massive flow of data the world produces every day.
There are also a variety of potential pitfalls, so businesses should be patient. The concept is still in its early stages, it can be a useful tool for many industries.
0 Comments